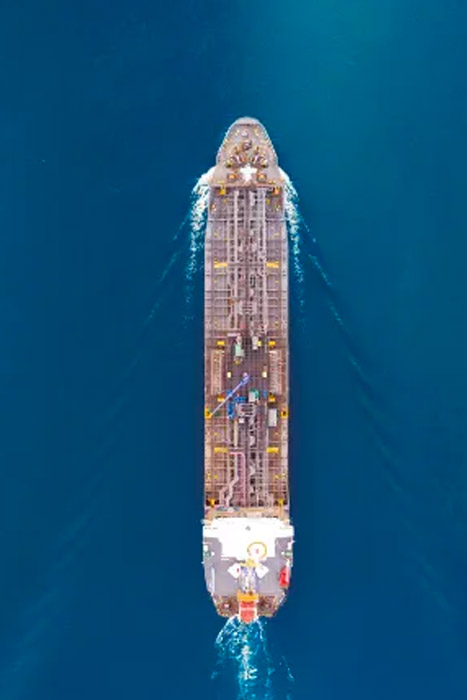
Why Nearshoring Is Not Going as Fast as You Want: Part 2
But there’s another equally valid reason why implementing a nearshoring strategy isn’t as easy as it might seem.
Keep reading to find out what it is.
Rise and Fall: Challenges with North American Manufacturing
Based on USMCA requirements, domestic content needs have risen from 62.5% to 75%. Good news, right? Well, yes—and no.
Yes, because this increase means there’s a greater need for domestic capacity in North America. And, no, because labor costs are high while availability of skilled labor remains tight. As such, experts expect U.S. manufacturing to continue its decline for many years to come.
But what about Mexico? Might Mexico be the beneficiary of (and savior from) this turmoil?
Unfortunately, the answer is “no.”
Right now, Mexico is ill equipped to increase its manufacturing capacity. In Mexico, die castings, injection molding, forgings, machining, rubber & plastics manufacturing—all of it—continue to be in short supply.
The Real Problem? Capital Costs!
One of the biggest reasons why suppliers in Mexico are unable to increase capacity is this: an inability to secure financing. You only have to look at interest rates as proof. Take, for example, the Bank of Mexico, which increased its interest rate by 50 bps, pushing it all the way up to a whopping 11%.
Undoubtedly, this is an extremely high and unsustainable cost factor for suppliers. Without question they would have to imbed this cost into their piece prices—yet still remain competitive.
Additionally, much of the financing that is available for real estate, working capital, and equipment come in the form of U.S. dollars. The problem with this is that it ups the ante for suppliers, who must justify capital costs as much as they do inputs, such as labor and maintenance.
As if that weren’t enough, Mexico’s currency, the peso, has been hit by a very high rate of inflation. Why just last year, Mexico’s rate of inflation came in at well over 7%!
What to Do About Costs
These many dynamics make it virtually impossible for suppliers to have the confidence or financial capability to invest in building capacity. Still, some are doing so cautiously. But, rest assured, this small rate of investment is unlikely to support the big market demands of the next several years.
So, what to do?
OEMs and Tier 1 suppliers who are already engaged or plan to engage in nearshoring, must (1) understand that cost is a crucial element and (2) be proactive about it. For capacity to grow, they must initiate open, honest dialogue with their suppliers, making sure to be very transparent in their cost discussions so they can help de-risk these much-needed suppliers.
Of course, we’ll continue to monitor nearshoring trends and share our perspective here. But, if you’d like to know how we’ve been proactive about growing our supplier base in North America, contact us. We have lots to share.
In case you missed it, be sure to check out part 1 for the other reason nearshoring can be a struggle.
Resources: