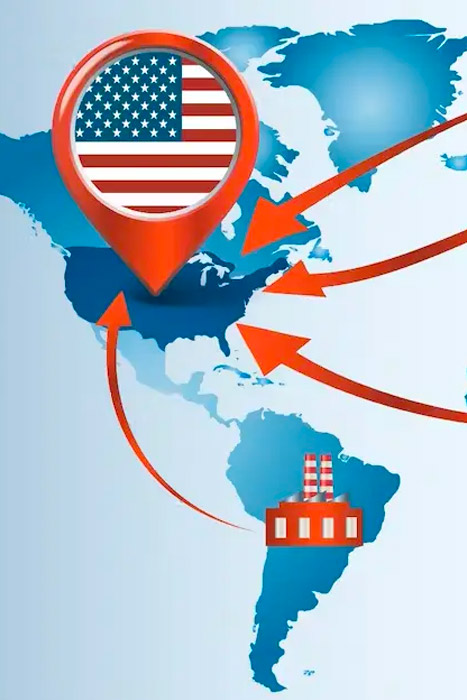
Why Nearshoring Is Not Going as Fast as You Want: Part 1
Kearney also says there are strong indications that that the gap between those that want to move their operations and those who are doing will soon begin to close.
What Is Nearshoring?
Put simply, nearshoring is when a manufacturer moves all or part of its long-distance operations to a location closer to home base.
For years, U.S. companies have sent their product manufacturing overseas to low-cost countries (LCC), such as Asia or India. Now, however, according to Kearney’s research, there’s a marked trend toward manufacturing returning to North America.
Why Nearshoring?
Just as there were many good reasons to shift U.S. manufacturing overseas to LCCs (cost being one of them), now there are many good reasons for the return. The biggest being the near catastrophic disruptions to the global supply chain.
With nearsourcing, the supply chain automatically becomes tighter, making it less vulnerable to such things as port shutdowns, shipping container issues, and dock worker shortages.
Nearshoring for Industrial Manufacturing
For industrial companies, the practice of nearsourcing holds great potential. Typically, resourcing for these companies involves finding Tier 1, 2 and 3 suppliers who have adequate capacity for not only manufacturing parts but also for developing the tooling and fixtures needed in making the parts.
The fact is the tool & die shop market is highly fragmented. Worse, the data around it is even less available.
Here’s what we know for sure about the market and its standing:
- According to a 2014 ETMM survey, there were 40,000 tool & die manufacturing enterprises in China.
- According to this same survey, these enterprises employed approximately 1 million skilled workers.
- Currently, there are only about 500 to 600 charted tool & die shops in Mexico.
- According to Zippia, there are only 54,248 tool & die makers in the U.S.
Suffice it to say, the tool & die market in North America is slim. Very slim, indeed.
So, for industrial customers looking to resource their component needs, it would seem there are only two ways to go:
- Obsolete the long tail. How? By manufacturing only high-mix-low-volume components. This approach would enable engineers to consolidate designs and use common parts to reduce the sheer complexity of their supply chains.
- Build their own tools and dies. Unfortunately, this approach is not just difficult but also expensive and time-consuming. For many, it would require rebuilding their component needs in the U.S. and in Mexico.
The Numbers Don’t Add Up
Of the almost 200+ RFQs sent by our firm in 2022 for a variety of die-castings, the majority came in with tool prices that were two to three times the cost of China. Not only that, lead times were twice those of China.
Resources:
- https://www.kearney.com/operations-performance-transformation/us-reshoring-index?utm_medium=pr&utm_source=prnewswire&utm_campaign=ReshoringIndex
- https://www.amtonline.org/article/mold-and-die-manufacturing-dawning-of-a-new-industry-in-mexico-part-i
- https://www.etmm-online.com/china-to-play-a-key-role-in-the-future-world-of-tooling-a-520855/?p=2